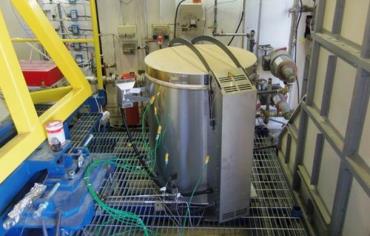
Prototype of the the excess heat system setup. Photo: COURTESY NEW CO2FUELS
Excess heat squandered in industrial production processes, as well as the carbon dioxide and water vapors emanating from their chimneys, will soon be put to positive use by an Israeli start-up.
The Rehovot-based NewCO2Fuels (NCF) plans to use the extreme heat released by factories such as steel, ceramics, glass and gasification plants – where residual heat temperatures rise to 1,450°C – to drive an innovative fuel production process, the company’s CEO, David Banitt, told The Jerusalem Post this week.
Through a process of electrolysis, catalystand membrane-laden cells capture the CO2 and water these factories emit, generating the highly potent syngas (a mixture of hydrogen and carbon monoxide) and a separate stream of oxygen.
While the heat used to drive this process originally came from solar sources – and still does in the company’s proof-of-concept laboratory at the Weizmann Institute of Science – the scientists feel that recycling the energy from the process itself would make this configuration a more marketable mechanism.
“What we found out is, there’s a lot of heat in the industry not used, and we could use that heat as well to drive our process,” Banitt said.
“We are moving more to exploit the high temperature excess from those industries.”
NCF acquired the original technology in 2011 from Yeda, Weizmann’s commercial branch.
The technology was developed by Prof. Jacob Karni’s laboratory in the department of environmental sciences and energy research, where Karni heads the institute’s Energy Center and supervises solar programs. His research, which he conducted in partnership with Dr. Avner Rothschild from the Technion-Israel Institute of Technology, received a $200,000 grant from the Silicon Valley-based Israel Strategic Alternative Energy Foundation in 2010. Karni serves as a consultant to NCF, while the company continues to fund research at laboratories in the Weizmann Institute that are further developing this technology.
NCF receives financial backing from the Australian firms GreenEarth Energy Ltd. and Erdi- Fuels, and is seeking additional investors.
Logistically the process involves a reactor made up of a single apparatus of cells, each with a membrane sandwiched between two catalyst layers, Banitt explained. The carbon dioxide enters and splits due to the extreme heat, with carbon monoxide exiting through one pipe and oxygen through a second. The same process is applied to water, yielding hydrogen and oxygen.
The hydrogen and carbon monoxide can then come together to form syngas, which in turn can be converted into fuels like methanol or plastics.
“You can look at it as a reverse combustion,” Banitt said.
Although it has already been proven that the process can be powered by the excess industrial heat, NCF’s proof-of-concept laboratory in the Weizmann Solar Tower runs primarily on solar heat, Banitt told the Post during a tour of the tower laboratory. The solar heat generation occurs via parabolic dishes, which reflect the light they capture to a reactor high up in the tower. This allows for extremely high temperature generation.
An advantage of using released industrial heat rather than solar energy is that the former is released 24 hours a day, while solar energy heat can only be generated between eight and 10 hours daily, Banitt noted. In addition, he said, most of the production cost in the former case is associated with the capital cost of the plant.
Looking at the steel, glass and ceramics industries, scientists at NCF realized that companies were wasting a lot of money: In order to produce their chimneys out of cheap materials rather than out of ceramics capable of withstanding extreme heat, the factories would pump in cold air to cool down the hot air released, according to Banitt.
“We tell them, give us this heat, and we will produce fuel from it,” he said. “They have heat – they do nothing with it right now.”
Insisting that the process was profitable, he stressed how huge the market was for syngas derivatives such as methanol, olephines, gasoline, diesel, ammonia, urea and many other chemicals. As an example, his company calculated that by generating methanol from the process, a plant could have a four-year payback on its investment, he said. In addition, he noted, the process operates with very high energy efficiency: The efficiency rate from heat energy to chemical energy in generating syngas is 40%.
“This is the key to being profitable,” he asserted.
During the conducted test runs, NCF found that out of 15 kg. of CO2, the company’s smallscale prototype could produce 10 kg. of carbon monoxide, he explained.
In terms of NCF’s path to commercial operation, Banitt said the company had signed a memorandum of understanding last week with two companies in Europe – the largest steel manufacturer in the world, and an engineering and equipment supplier. Together, the team plans to build a demonstration and pilot plant in Belgium, and an official agreement will be solidified within a year, he said. He added that if all went as planned, the European project would kick off in about 18 months.
In addition to taking part in this understanding, NCF has agreed to collaborate with an international company that focuses on energy- intensive equipment, in order to apply for a project grant from the United States Department of Energy. The two firms plan to test their products together, and upon success, to integrate the two, Banitt said.
“Now that we are getting more and more reassurance from the market that what we are proposing to them has real economic potential, we are more confident that we are doing the right thing,” he added.